SOLDER BARS AND ANODES
Our solder and tin anodes are processed for high density and
fine grain structure, and are the highest quality anodes available
to the printed circuit board industry. These solders are designed
and engineered to meet Indian, British, German, Japanese and
American specifications. A unique processing method used in
manufacturing these anodes eliminates oxide and non-metallic
inclusions, and provides uniform plating without sludging
and flaking.
These solders can be used for general soldering applications
as well as for critical microelectronic assemblies. They can
be used in all types of automatic soldering machines, dip
soldering equipment, tinning baths and all manual soldering
processes. The anodes can be used to plate printed circuit
board to extend the solderable shelf life and to use as an
etch resist. They are also applicable for plating copper wire,
bus bar as well as for plating terminals, eyelets and other
electronic components. These solders and anodes are processed
to assure fine grain structure and even dissolution during
soldering or plating.
SOLDER PAINT
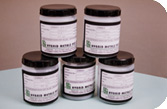
Hybrid # RAD 3400 Solder Paint is formulated for Reflow soldering of Radiators, Heat exchangers, Sheet Metal Soldering and automobile body patching applications.
Hybrid Solder Paint is a well-homogenised suspensions of solder particles in an active flux system. The solder used in manufacturing Hybrid Solder Paint is pre-alloyed before atomization to assure accurate melt ranges and qualify reliable wetting to the base metal surfaces. Hybrid Solder Paint offer dependability and economy. It can be used efficiently for mass soldering of radiators and heat exchangers.
Hybrid Solder Paint is normally applied by brush. Solder Paint can be melted and re flowed with any heat source. Soldering time and temperature are dependent on alloy composition and type of flux. Hybrid Solder Paint is available in a proprietary alloy composition suitable for these applications.
SOLDER WIRE
We
manufacture solders in wire form, solid, single core and multi-core
(up to five core) from 8mm to 26SWG in standard compositions.
Cored solder wires are produced with various core percentages.
They are available with non activated (R), mildly activated
(RMA), fully activated (RA) and water soluble flux core. We
also supply wires with acid core, urea core or any other type
of flux core according to customer requirements. Advanced
no-clean core wire up to 0.5mm diameter is also available
upon request. The solder alloy composition, wire diameter,
flux quality and percentage of flux in the wire is monitored
and controlled to provide consistent results. Our solder wires
are suitable for hand soldering of electronic assemblies.
The very low impurity levels assure strong and clean solder
joints of high reliability.
RMA RESIN FLUX
CORE SOLDER WIRE
RMA
type resin-core solder wire has been developed for use in
electronics industry and meets the chemical and metallurgical
requirements specified in various industry and international
standards. Our RMA type resin flux used in manufacturing RMA
flux cored solder wire is an extremely effective flux which
provide very high reliability solder joint. The residue left
after soldering is non-corrosive, moisture and fungus resistant
and is considered to be non-conductive. The residue after
soldering need not to be removed in most cases. This is a
high reliability flux core solder wire and is suggested to
be used in military, telecommunication, computer, aeronautics
and other critical applications.
RA RESIN FLUX CORE SOLDER WIRE
RA type resin cored solder wire is available in all type of
solder alloys, different sizes and varying core percentages.
It is used for soldering any kind of electronic assemblies.
It provides instant wetting and excellent capillary action
which results in less rejections and few touch-ups. This type
of wire is suitable for soldering oxidized and difficult to
solder metals. The flux residue left after soldering is considered
to be non-conductive non-hygroscopic and non-tacky, and can
be removed by, solvent cleaning process.
WATER SOLUBLE FLUX
CORE SOLDER WIRE
Water
soluble core solder wire is an aggressive organic core solder
specifically for soldering electronic assemblies, particularly
applicable for use where acid core flux is too corrosive and
rosin fluxes are too inactive. Water soluble core solder is
suitable for soldering heavily oxidized metal surfaces. Water
soluble core flux is an active flux and should be removed
after hand soldering operation. The residue can be readily
and completely removed with water or aqueous detergent cleaner.
NO-CLEAN FLUX CORE
SOLDER WIRE
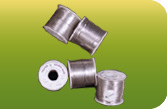
No-clean cored solder wire was developed to eliminate the
use of solvents for post-solder cleaning of circuit board
assemblies in electronic industry. The No-clean flux used
in the wire core is completely halide-free and meets the requirements
specified in Bell Core specification and J-STD-004. It provides
excellent solderablity and high reliability. The flux residue
requires no cleaning due to physico-chemical characteristics
of the core flux.
SOLDER PASTE
AIM’s full line of no clean solder products and water soluble solder products includes solder pastes, liquid fluxes and cored wire solders. These products have been proven to provide excellent soldering results to the end user
AIM’s No Clean Solder Pastes and Water Soluble Solder Pastes are available in a variety of alloys, particle sizes, metal contents and viscosities designed to suit all SMT applications. AIM solder pastes are produced from the highest quality, oxide-free powder manufactured to the ElectropureTM Specification. These are each available in a wide selection of packaging, including jars, cartridges, syringes and ProFlow cassettes.
AIM’s Water Soluble Solder Pastes at a Glance
• Lead-Free and Tin-Lead Compatible • Excellent Wetting • Superior Slump Resistance • Aqueous Wash with Water
• Extended Cleaning Window • Large Process Window • Printing and Dispensing Formulas • Excellent Print Characteristics
• Very Good Activity • Extended Stencil Life and Tack Time
AIM’s No Clean Solder Pastes at a Glance
• Lead-Free and Tin-Lead Compatible • Halogen- and Halide-Free • Excellent Wetting • No Head-in-Pillow • Low Tombstoning
• Clear Pin-Probe Testable Residue • Extended Stencil Life and Tack Time • Eliminates Voiding • Low Solder Beading
• Printing and Dispensing Formulas
PRODUCT NO |
ALLOY
COMPOSITION
|
COMMON
REQUREMENTS |
SOLIDUS
|
LIQUIDUS
|
|
Sn |
Pb |
Ag |
Bi |
Cu |
Zn |
BAR |
WIRE |
PASTE |
PAINT |
°C |
°C |
1 |
5 |
95 |
- |
- |
- |
- |
|
|
- |
- |
308 |
312 |
2 |
5 |
93.5 |
1.5 |
- |
- |
- |
|
|
- |
- |
287 |
296 |
3 |
10 |
90 |
- |
- |
- |
- |
|
|
- |
- |
275 |
302 |
4 |
10 |
88 |
2 |
- |
- |
- |
|
|
|
- |
267 |
299 |
5 |
15 |
85 |
- |
- |
- |
- |
|
|
- |
- |
183 |
288 |
6 |
20 |
80 |
- |
- |
- |
- |
|
|
- |
- |
183 |
280 |
7 |
25 |
75 |
- |
- |
- |
- |
|
|
- |
- |
183 |
268 |
8 |
30 |
70 |
- |
- |
- |
- |
|
|
- |
|
183 |
257 |
9 |
40 |
60 |
- |
- |
- |
- |
|
|
- |
|
183 |
238 |
10 |
43 |
43 |
- |
14 |
- |
- |
|
|
|
- |
144 |
163 |
11 |
49 |
51 |
- |
- |
- |
- |
|
- |
- |
- |
183 |
216 |
12 |
50 |
50 |
- |
- |
- |
- |
|
|
- |
- |
183 |
212 |
13 |
60 |
40 |
- |
- |
- |
- |
|
|
- |
- |
183 |
191 |
14 |
62 |
36 |
2 |
- |
- |
- |
|
|
|
- |
179 |
179 |
15 |
62 |
38 |
- |
- |
- |
- |
|
|
- |
- |
182.7 |
183.3 |
16 |
63 |
37 |
- |
- |
- |
- |
|
|
|
|
183 |
183 |
17 |
65 |
35 |
- |
- |
- |
- |
|
- |
- |
- |
183 |
192 |
18 |
70 |
30 |
- |
- |
- |
- |
|
- |
- |
- |
183 |
193 |
19 |
75 |
25 |
- |
- |
- |
- |
|
|
- |
- |
183 |
194 |
20 |
75 |
- |
- |
- |
- |
25 |
|
|
- |
- |
- |
MP
300 |
21 |
80 |
- |
- |
- |
- |
20 |
- |
- |
- |
- |
- |
MP
280 |
22 |
80 |
20 |
- |
- |
- |
- |
|
|
- |
- |
183 |
199 |
23 |
95 |
5 |
- |
- |
- |
- |
- |
|
- |
- |
183 |
222 |